
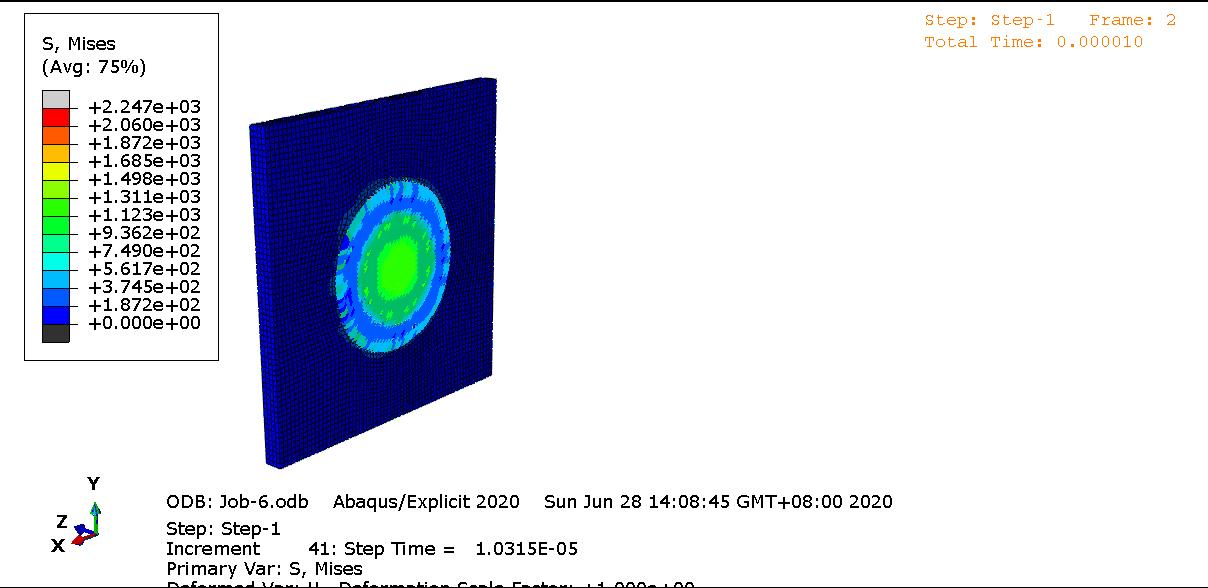
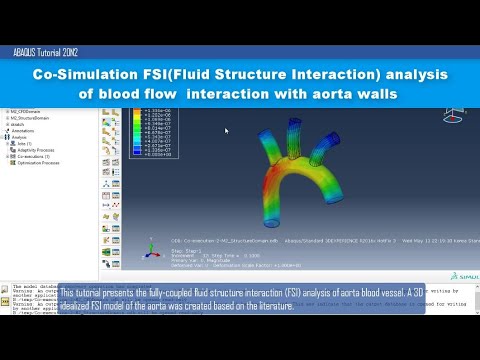
This is an exciting direction from the makers of Abaqus, considered by many to be the high-end of high-end finite element analysis (FEA) products. Studies using a viscoelastic tire model are planned for future work.SIMULIA, the Dassault Systèmes brand for simulation based out of Providence, RI, wants to democratize multiphysics, or MP. Note that the tire is modeled as a rigid body in the present simulation. Some granular material remains in the groves of the tire profile. The sticky granular material is compacted by the tire motion which causes a torque slowing down the rotation. The particles are color coded according to their velocity magnitude ranging from blue (zero velocity) to red (highest velocity).
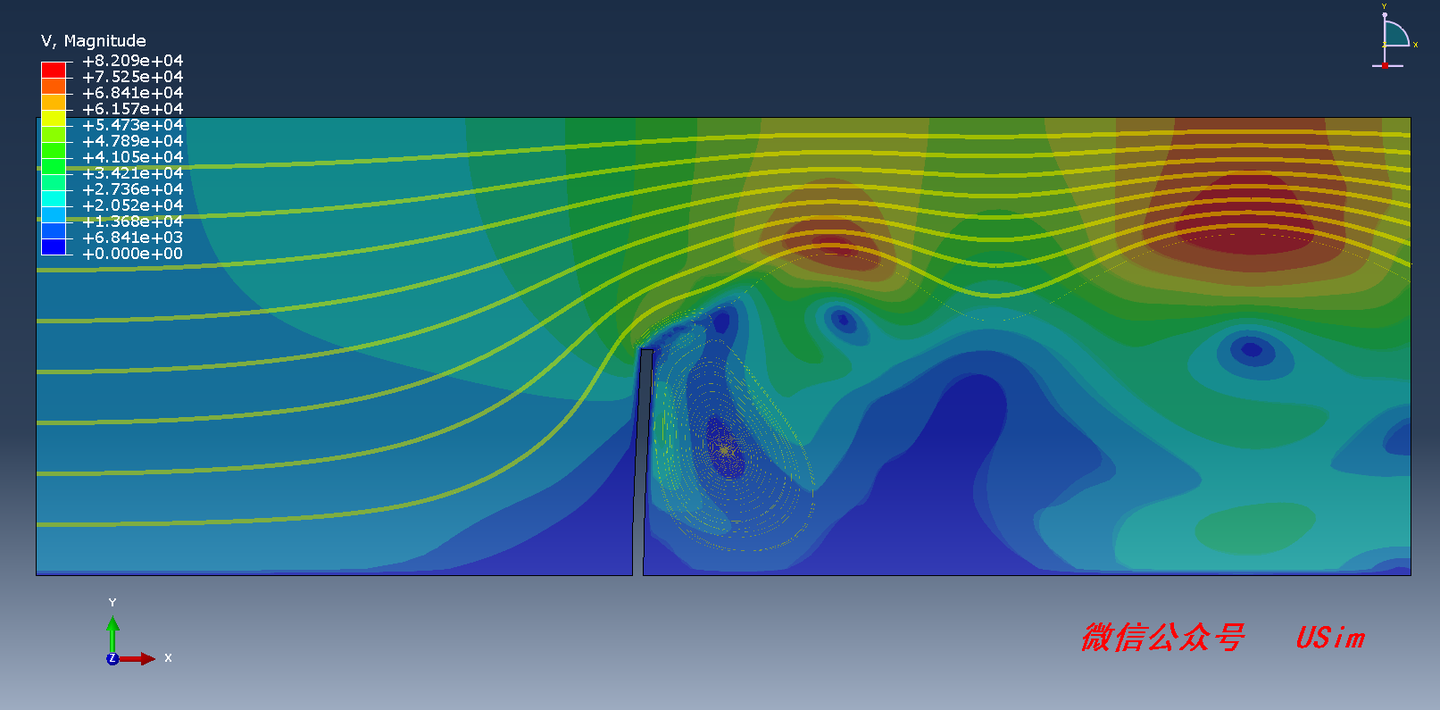
The figure below shows a series of simulation snapshots. A constant torque is applied on the tire which is initially at rest. In the present case a strong cohesion is used to make the particles very sticky.
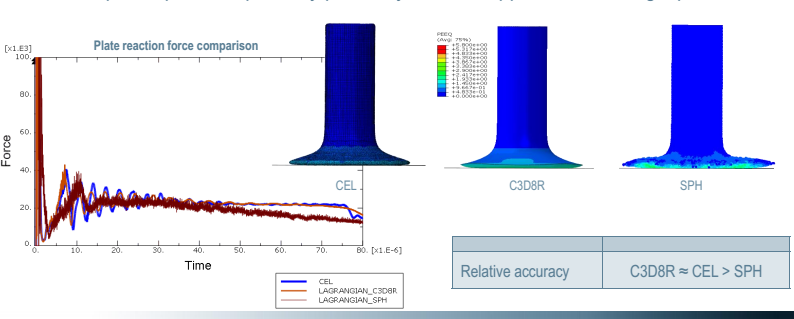
The DEM force laws can be parameterized in order to represent various types of grounds ranging from sand over mud to snow. The implementation of such a co-simulation scheme has been realized using SimPARTIX®, the FEA software Abaqus/Explicit and a communication interface developed at the Fraunhofer SCAI.Ī possible application for the developed co-simulation scheme is the traction of a tire on a granular ground. Displacements and velocity are therefore sent back from the FEA code to the particle code. The FEA results are new nodal displacements and nodal velocities, which on their part are the input to the particle code describing the motion of the coupled wall. These forces are the structural load applied to the FEA model. The particles, hitting the wall, cause reaction forces at the wall, e.g., due to repulsion, cohesion and damping as well as tangential friction. The coupled walls on the structural side are in fact all parts, which may get in contact with the particles during the simulation at any time.Īt the coupled walls, elastic and kinetic energy as well as momentum are exchanged between the structure and the particles. In this surface coupling method these walls are the domain boundaries of each numerical model. Co-simulations using smoothed particle hydrodynamics (SPH) and FEA are useful to model fluid-structure interaction (FSI) phenomena including large deformations.Ĭo-simulation in the cases presented here means the controlled exchange of quantities on the coupled walls between two different simulation codes at each time step. The possibility of coupling discrete element method (DEM) and finite element analysis (FEA) simulations is particularly attractive in order to model contact between granular matter and soft bodies.
